Plastic Molding Electrical: Revolutionizing Manufacturing
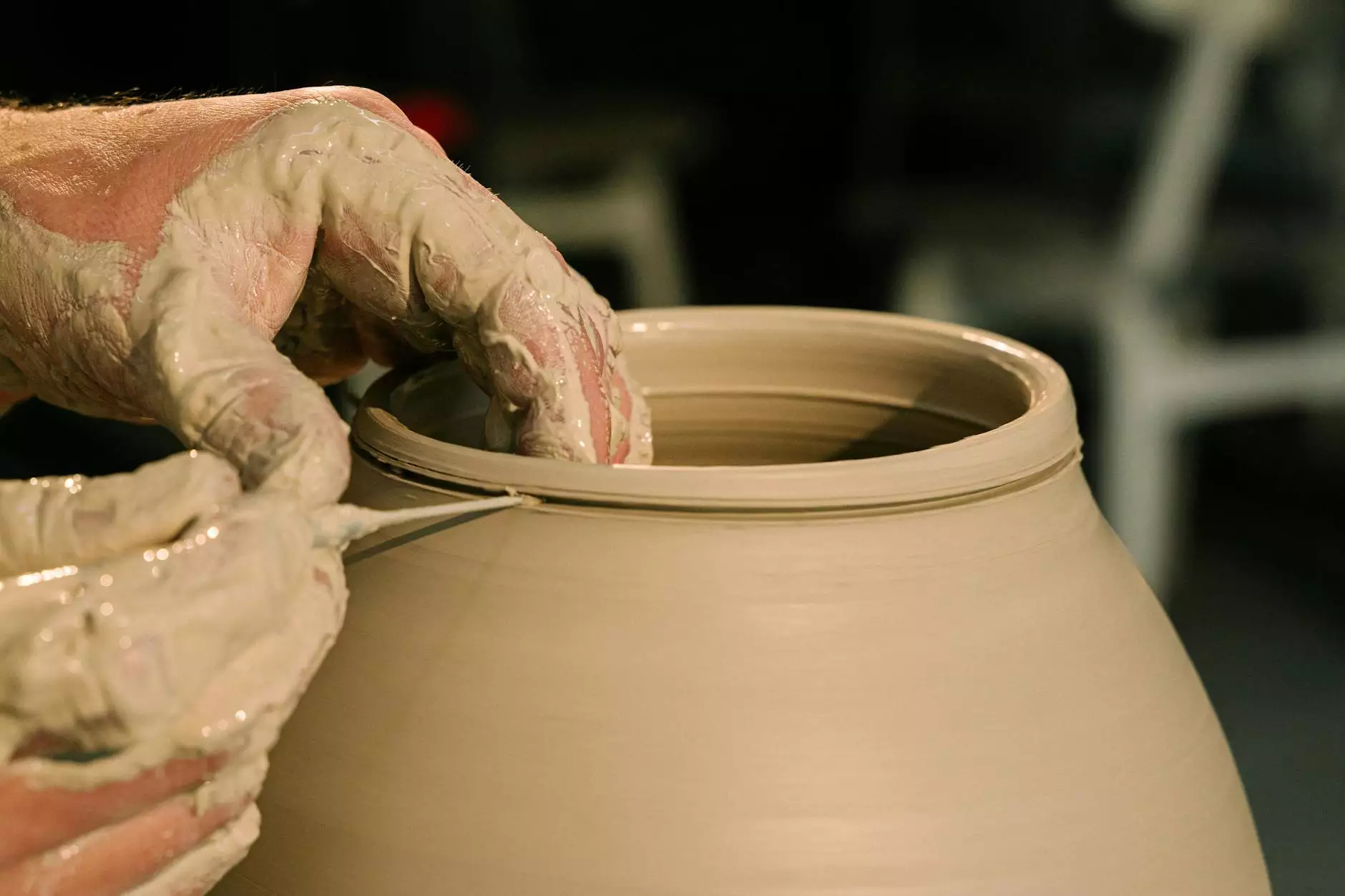
Plastic molding electrical technologies are at the forefront of modern manufacturing, merging efficiency and innovation to yield remarkable products that meet the demands of various industries. This article delves deeply into the intricacies of plastic molding in the electrical sector, its numerous advantages, applications, and future trends that promise to shape the landscape of manufacturing as we know it.
Understanding Plastic Molding
At its core, plastic molding is a manufacturing process that involves the shaping of plastic materials into defined geometries. The process begins with the melting of plastic pellets, which are then injected into a mold to take the desired shape. Once cooled, the molded part is ejected, allowing for rapid production of high-quality components.
In the sphere of electrical components, plastic molding electrical becomes particularly significant. Electrical components often require precise engineering to ensure functionality, safety, and durability. Thus, the role of plastic molding cannot be overstated.
The Key Benefits of Plastic Molding in Electrical Manufacturing
The utilization of plastic molding in the electrical industry offers numerous advantages, which can be summarized as follows:
- Cost-Effectiveness: Plastic molding is generally less expensive than metal fabrication processes, leading to reduced production costs.
- Precision and Consistency: This process allows for high precision, ensuring that every cut, shape, and detail is uniform across all produced parts.
- Lightweight Products: Plastic components are significantly lighter than their metal counterparts, making them ideal for applications requiring reduced weight.
- Complex Shapes: Advanced molding techniques enable the creation of complex geometries that would be challenging or impossible to achieve through traditional machining.
- Enhanced Insulation: Plastics offer superior electrical insulation, making them a natural choice for many electrical applications.
Applications of Plastic Molding in the Electrical Sector
The applications of plastic molding electrical are vast and varied. Here are some of the primary areas where this technology is making a significant impact:
1. Electrical Enclosures
One of the primary applications is in the production of electrical enclosures, which require robust, durable, and insulation properties. Plastic molded enclosures protect sensitive electrical components from environmental elements such as moisture, dust, and abrasive particles.
2. Connectors and Terminals
Plastic molding is often utilized for creating connectors and terminals that are integral to electrical systems. These components need to feature intricate designs, ensuring secure connectivity while maintaining reliable insulation to prevent short circuits.
3. Switches and Control Devices
Another critical application is in switches and control devices. The demand for various toggle switches, push buttons, and rotary switches necessitates high-volume production techniques that offer precision and reliability, which plastic molding effectively addresses.
4. Insulating Components
Given the electrical nature of components, the insulation properties of plastics make them indispensable in the manufacturing of insulating parts that prevent electrical leakage and enhance system safety.
5. Housing for Circuit Boards
Plastic molding is also essential in creating housings for circuit boards, which require precise dimensions to fit various electronic components securely while allowing for adequate heat dissipation.
Advanced Techniques in Plastic Molding Electrical Manufacturing
As technology continues to evolve, so do the methods of plastic molding electrical manufacturing. Here are some of the advanced techniques that are shaping the future:
1. Injection Molding
This widely used method allows for rapid production with intricate designs and excellent repeatability, making it ideal for mass production of electrical components.
2. Blow Molding
Blow molding is primarily used for creating hollow plastic parts, making it beneficial for specific electrical enclosures that require a lightweight yet robust design.
3. 3D Printing in Molding
3D printing technology is revolutionizing the way molds are created. Rapid prototyping enables faster turnaround times for design adjustments and testing, ultimately expediting the development process.
4. Overmolding
This technique combines multiple materials in a single part, enhancing functionality, aesthetics, and tactile feedback for electrical devices.
The Role of Quality Control in Plastic Molding Electrical
Quality control is vital in the manufacturing process of electrical components. As standards for electrical safety and performance continue to rise, stringent testing and inspections become necessary to maintain quality assurance. Key quality control measures include:
- Material Verification: Ensuring that the right type of plastic is used for specific applications is critical to maintaining safety and performance standards.
- Dimensional Accuracy: Regular measurements are taken to confirm that produced components meet specified tolerances.
- Electrical Testing: Advanced electrical testing methods assess insulation resistance, dielectric strength, and current-carrying capacity.
- Visual Inspections: A thorough inspection for surface defects and dimensional integrity is essential to avoid failures in end applications.
Challenges Faced in Plastic Molding Electrical Manufacturing
Despite its many advantages, the plastic molding electrical industry does encounter some challenges that manufacturers must navigate:
1. Material Limitations
Some plastics may not withstand extreme temperatures and environmental conditions, limiting their application in certain electrical environments.
2. Design Complexity
While most shapes can be achieved, overly complex designs can lead to production inefficiencies and increased costs.
3. Sustainability Concerns
With growing awareness of environmental impact, many manufacturers are pressured to seek sustainable practices and explore recyclable materials to reduce waste.
Future Trends in Plastic Molding for Electrical Components
The future of plastic molding electrical holds exciting prospects:
1. Sustainable Materials
The shift towards eco-friendly materials is gaining traction, with innovations in biodegradable and recyclable plastics becoming more prevalent in manufacturing processes.
2. Smart Manufacturing
Integrating smart technologies, like IoT and AI, can streamline the production process, predict maintenance needs, and enhance overall productivity and accountability.
3. Advanced Customization
Customization options are expanding, empowering clients with the capability to choose specific designs, materials, and functionalities tailored to their unique needs.
4. Increased Automation
Automation in production lines is set to enhance efficiency further, reduce human error, and speed up production timelines while maintaining quality standards.
Conclusion: The Promising Landscape of Plastic Molding Electrical
In the ever-evolving world of manufacturing, plastic molding electrical technologies are establishing themselves as a cornerstone for innovation, quality, and efficiency. By understanding the various benefits, applications, and future trends associated with this technology, businesses can position themselves at the forefront of the manufacturing landscape.
As industries continue to demand higher quality and customized solutions, the adaptability and advantages presented by plastic molding will ensure its crucial role in the future of electrical manufacturing.
For more innovative solutions in manufacturing, visit DeepMould.net.