Exploring Die Casting Machine Parts: A Comprehensive Guide for Metal Fabricators
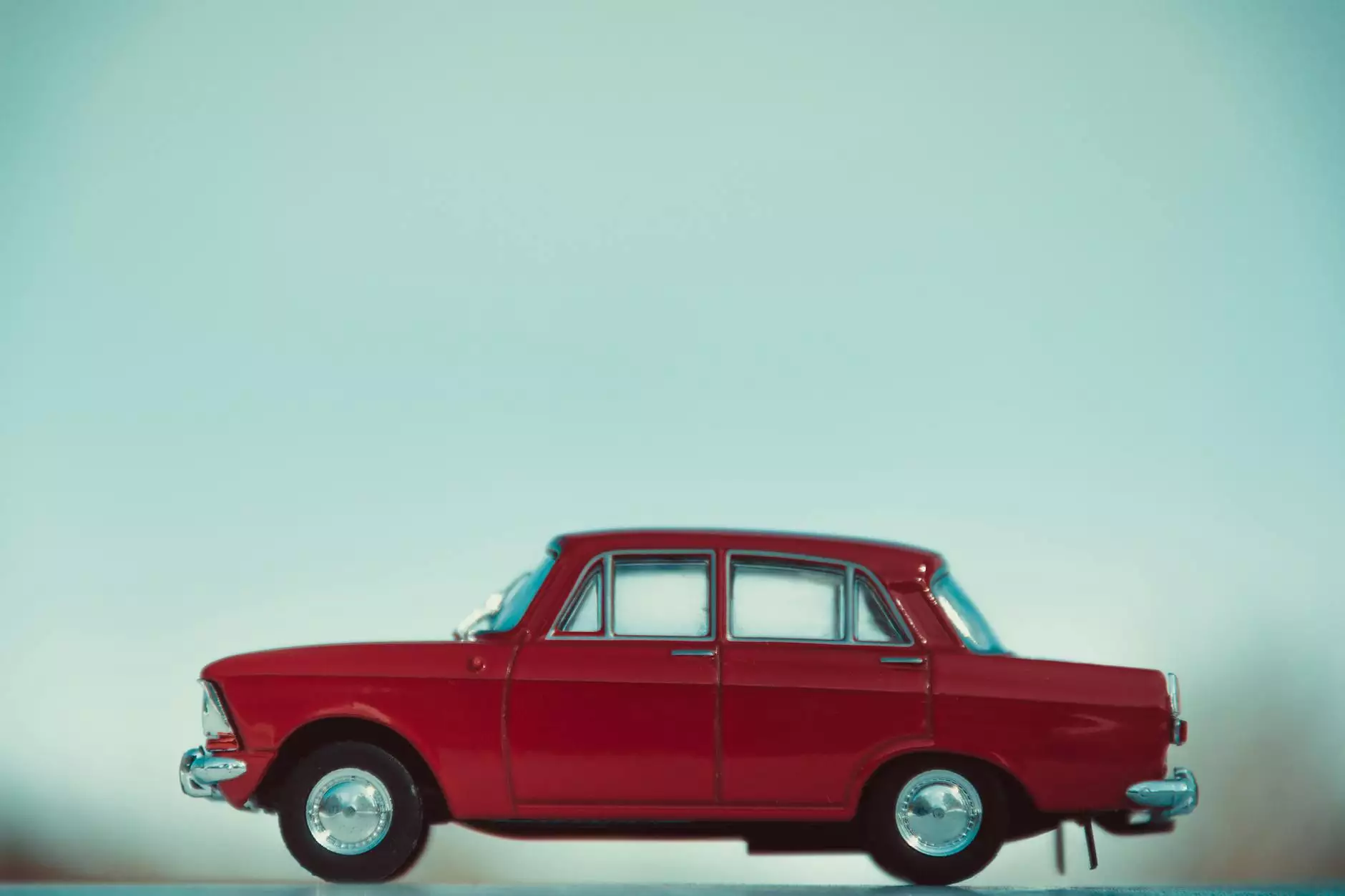
In the world of metal fabrication, precision and efficiency are paramount. One of the most critical components of this industry is the die casting machine parts. This comprehensive guide will delve into the significance, functionalities, types, and advantages of these essential components, helping metal fabricators understand their importance in enhancing the manufacturing process.
Understanding Die Casting: The Basics
Before diving into die casting machine parts, it’s essential to understand what die casting is. Die casting is a manufacturing process used to produce metal parts by forcing molten metal under high pressure into mold cavities. The result is high-precision components that are often used in automotive, aerospace, and consumer goods industries.
Ultimately, the die casting process produces parts that are not only durable but also exhibit excellent surface finish and dimensional accuracy. The key to unlocking the full potential of this process lies in the effectiveness of its machine parts.
Key Components of Die Casting Machine Parts
Die casting machines are complex units made up of numerous parts that work in unison. Understanding these components is crucial for any metal fabricator looking to enhance their manufacturing capabilities. Below are the main parts of die casting machines:
- Injection System: This is the heart of the die casting machine. It injects molten metal into the die at high pressure. The design and efficiency of the injection system significantly impact the quality of the produced parts.
- Die Block: The die block contains the mold and is responsible for shaping the molten metal. It consists of two halves - the A-side (fixed) and B-side (movable) - ensuring that the casting solidifies correctly.
- Ejector System: Once the metal has cooled and solidified, the ejector system uses ejector pins to remove the cast from the die without damaging it. This system plays a critical role in maintaining the speed of production.
- Clamping Unit: This unit holds the die in place during the injection of molten metal. The clamping force must be adequately adjusted to prevent the die from opening under pressure during injection.
- Cooling System: A consistent temperature is vital for the die casting process. The cooling system helps maintain the temperature of the mold, ensuring that the metal solidifies correctly and that the die maintains its shape.
- Controller and Sensors: Modern die casting machines come equipped with advanced controls and sensors that monitor temperature, pressure, and other parameters to optimize the production process.
The Benefits of Quality Die Casting Machine Parts
Investing in high-quality die casting machine parts offers substantial benefits for metal fabricators. Here’s how superior components influence the production process:
1. Enhanced Product Quality
High-quality die casting machine parts ensure that the produced components are dimensionally accurate and possess excellent surface finishes. This quality translates into fewer defects and reworks, ultimately enabling fabricators to deliver superior products to their clients.
2. Increased Efficiency
Efficient die casting parts can significantly reduce cycle times. When components, such as the injection system and cooling system, function optimally, the machines can operate at a faster pace. This efficiency leads to greater productivity and profitability.
3. Cost-effectiveness
While investing in quality parts might initially seem like a significant expense, the long-term savings from reduced maintenance costs and fewer downtime events make this investment worthwhile. Moreover, high-quality components usually have longer service lives, further reducing replacement costs.
4. Versatility
Robust die casting machine parts can accommodate a wider range of materials and sizes for different applications. This versatility enables metal fabricators to diversify their offerings and meet customer demands more effectively.
Different Types of Die Casting Processes
Understanding the different types of die casting processes is crucial for fabricators seeking to maximize efficiency and quality. Here are the most common methods:
- Hot Chamber Die Casting: In this process, the molten metal is kept in a furnace and injected into the die from a chamber. It is primarily used for metals with lower melting points, such as zinc and magnesium.
- Cold Chamber Die Casting: Here, the molten metal is poured into the injection chamber before being inserted into the mold. This method is suitable for metals with higher melting points like aluminum and copper.
- Hybrid Die Casting: This innovative method combines both hot and cold chamber techniques to optimize the benefits of each, providing flexibility in production.
Choosing the Right Die Casting Machine Parts Supplier
Selecting a reliable supplier for die casting machine parts is crucial for ensuring quality and performance. Here are some essential factors to consider:
1. Experience and Expertise
Look for a supplier with a proven track record and extensive knowledge in die casting. Their expertise can guide you in selecting the best components for your specific needs.
2. Product Range
Choose a supplier that offers a wide range of parts. A comprehensive catalog can help ensure that you can source all necessary components from one place, minimizing procurement complexity.
3. Quality Assurance
Ensure that the supplier follows stringent quality control measures. Certification and compliance with international standards can be indicators of quality assurance.
4. Customer Support
Excellent customer service and technical support can be invaluable. Choose a supplier that offers guidance and assistance even after the sale, helping you optimize your production process.
Future Trends in Die Casting Technology
The die casting industry is continually evolving with advancements in technology. Here are some future trends that metal fabricators should pay attention to:
- Automation and Robotics: Integrating automation in die casting processes will enhance efficiency and accuracy, reducing labor costs while increasing output quality.
- 3D Printing for Die Casting: The use of 3D printing in creating molds can significantly reduce lead times and costs, and allow for complex geometries that traditional methods can’t achieve.
- Environmentally Friendly Practices: There’s a growing trend for sustainable die casting practices, focusing on recycling materials and reducing waste, promoting eco-friendly manufacturing.
Conclusion
In conclusion, die casting machine parts are vital for enhancing the efficiency, quality, and cost-effectiveness of metal fabrication processes. Understanding the components, choosing high-quality parts, and staying abreast of industry trends can position metal fabricators for success in a competitive landscape.
By focusing on these factors and investing wisely, businesses can ensure they are not just keeping pace but leading the way in the die casting industry, maximizing their productivity, and minimizing costs, thus fulfilling the demands of their clients more effectively.
For further information and resources on die casting machine parts and metal fabrication, consider visiting Deep Mould, where innovation meets quality in manufacturing.