Maximizing Your Product Development with Plastic Prototype Service
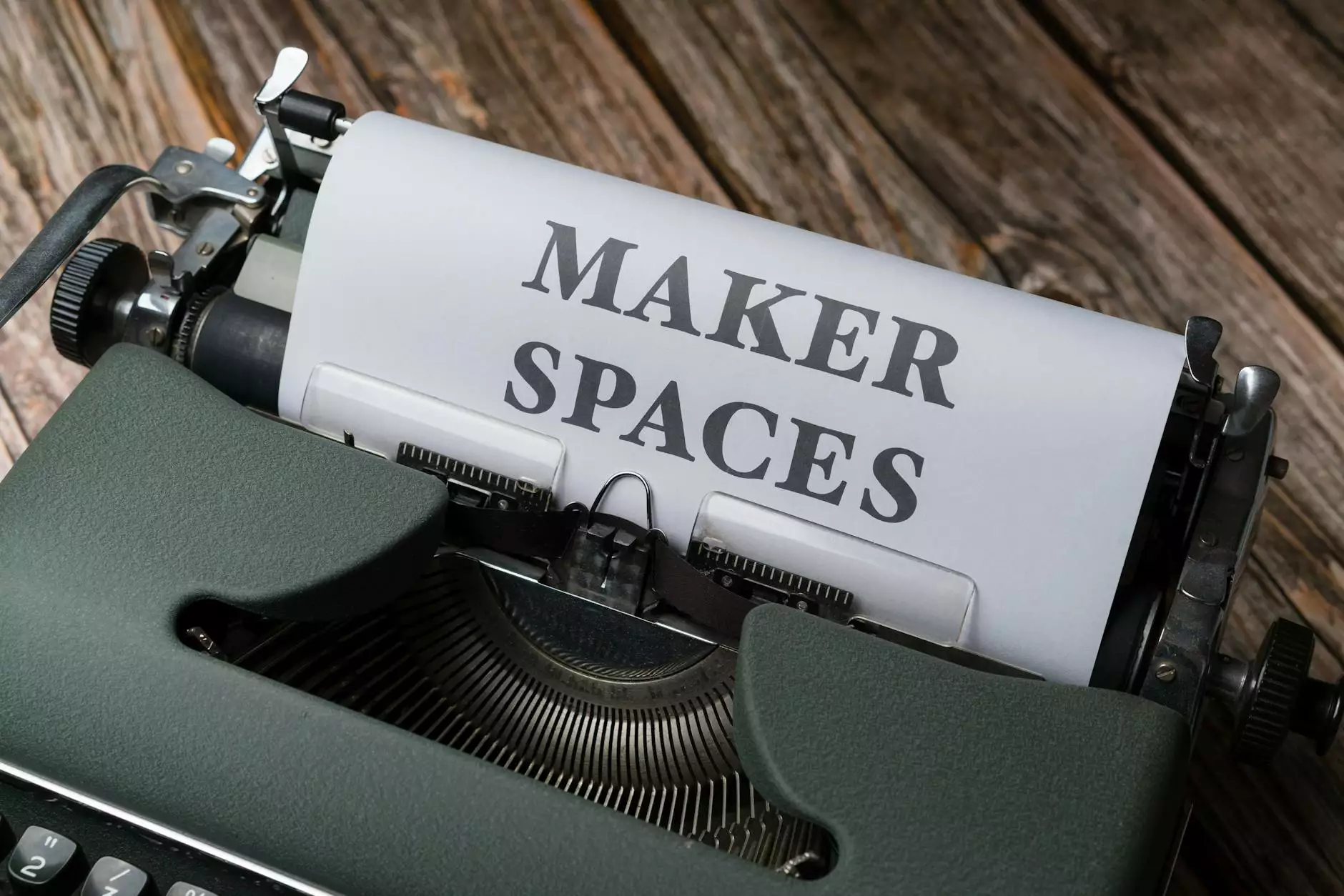
In the rapidly evolving landscape of business, the ability to prototype effectively is crucial. Enter the plastic prototype service—a pivotal element in modern product development that allows designers and manufacturers to create tangible versions of their concepts. This service offers significant advantages that can streamline operations, reduce costs, and enhance overall product quality.
Understanding Plastic Prototyping
Plastic prototyping involves the creation of physical models of products to evaluate designs before moving into mass production. This stage is critical for identifying flaws, testing functionality, and refining aesthetic elements.
Benefits of Using Plastic Prototype Service
- Cost Efficiency: Prototyping generally reduces the overall costs associated with production. By identifying and resolving issues early, companies avoid the significant expenses tied to reworking tooling or materials.
- Time-Saving: Rapid prototyping can shorten the development cycle significantly. This allows businesses to bring products to market faster than ever.
- Enhanced Communication: Physical prototypes can facilitate better communication between stakeholders, design teams, and clients, making it easier to visualize the end product.
- User Testing: Prototypes can be shared for user feedback, allowing designers to make informed decisions based on actual user experiences rather than assumptions.
- Innovative Design Iteration: Designers can quickly develop and test various design iterations, fostering an environment of innovation and creativity.
The Process of Plastic Prototyping
To fully appreciate the value of a plastic prototype service, it is essential to understand the typical stages involved. Here’s a detailed breakdown of the process:
1. Design Conceptualization
Initially, ideas and concepts are sketched out, often using computer-aided design (CAD) software. This digital representation serves as the foundation for the prototype.
2. Material Selection
The choice of materials is vital when considering the end use of the product. Selecting the right type of plastic—be it ABS, polycarbonate, or POM—can impact the durability, appearance, and functionality of the prototype.
3. Prototype Fabrication
Using advanced technologies such as 3D printing, CNC machining, or injection molding, manufacturers create the prototype. Each method has its unique benefits and is chosen based on factors like detail required, volume, and functionality.
4. Testing and Evaluation
Once the prototype is built, it undergoes testing. This phase is crucial as it provides insights into functionality, usability, and durability. Any feedback gathered is then incorporated into the next iteration of the design.
5. Finalization and Production
After refining the prototype based on testing feedback, the final design is prepared for mass production. This ensures that manufacturers move forward with confidence and clarity.
Applications of Plastic Prototype Service
The versatility of plastic prototypes means they are utilized across various industries, including:
- Consumer Electronics: From smartphone cases to home appliances, ensuring ergonomic designs that enhance user experience.
- Automotive: Rapid prototyping of components, interior parts, and even entire body designs helps in reducing the development time for new models.
- Medical Devices: Prototyping for complicated assemblies, ensuring that devices meet regulatory standards while also being patient-friendly.
- Toys and Games: Testing design and functionality before mass production can help ensure safety and playability.
- Household Products: From kitchen tools to furniture, prototyping helps manufacturers fine-tune product functionality and design.
Why Choose DeepMould for Your Plastic Prototype Service?
DeepMould, as a leader in the plastic prototype service market, stands out for several reasons:
1. Expertise and Experience
With years of experience in metal fabricators and prototype development, the team at DeepMould possesses the knowledge to handle a wide range of projects with various complexities.
2. State-of-the-Art Technology
DeepMould employs cutting-edge technology in its prototyping processes, ensuring high precision and quality. From 3D printing to advanced CNC machining, every method employed maximizes performance and efficiency.
3. Custom Solutions
Every project is unique at DeepMould. The skilled professionals work closely with clients to tailor solutions that meet specific needs, delivering prototypes that align perfectly with the vision.
4. Comprehensive Support
DeepMould provides end-to-end support, from initial concept discussions to final production, ensuring that every client receives vital input and guidance at each stage.
Conclusion
The importance of a reliable plastic prototype service cannot be overstated. For businesses seeking to innovate and stay competitive, integrating effective prototyping into the product development process is essential. With the capability to test, iterate, and enhance designs quickly, companies can streamline their efforts and deliver superior products to market.
Choosing a seasoned partner like DeepMould ensures that businesses leverage the full potential of prototyping services, minimizing risks and maximizing design efficiency. In an age where speed and quality matter more than ever, investing in plastic prototyping is a strategic move toward achieving manufacturing excellence.
Get Started with DeepMould Today!
If you are ready to elevate your product development process, consider partnering with DeepMould for outstanding plastic prototype service. Our experienced team is here to help you transform your ideas into reality, ensuring your concepts are not just imagined but expertly crafted as prototypes that pave the way for your product's success.