The Importance of Choosing the Right Die Casting Tool Manufacturer
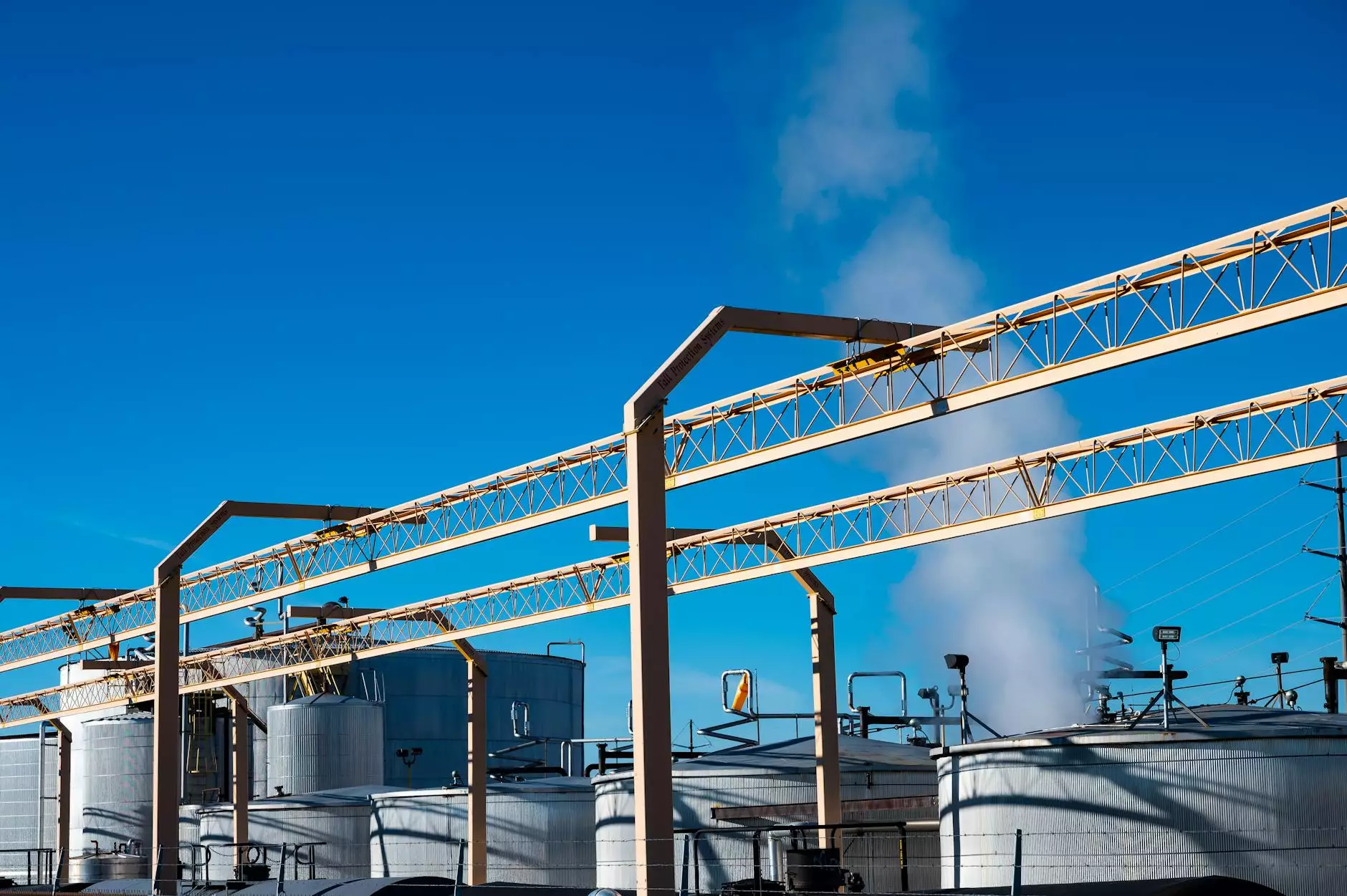
In the world of manufacturing, especially in sectors relying on metal fabrication, the tools used can significantly impact the final product's quality and efficiency. This is particularly true in the die casting industry, where precision and durability are paramount. Selecting the right die casting tool manufacturer not only enhances the production process but also ensures that the finished products meet the highest standards. In this article, we will explore various aspects of die casting, the critical role of choosing a quality manufacturer, and what you should consider in your selection process.
Understanding Die Casting
Die casting is a manufacturing process that involves forcing molten metal under high pressure into a mold cavity. This technique is ideal for producing parts with intricate shapes and superior dimensional accuracy. Common materials used in die casting include:
- Aluminum
- Zinc
- Magnesium
- Copper
These materials provide excellent strength-to-weight ratios, corrosion resistance, and finishing capabilities, making them ideal for various applications, including:
- Automotive components
- Consumer electronics
- Industrial machinery
- Aerospace parts
The Role of a Die Casting Tool Manufacturer
The die casting tool manufacturer plays a vital role in the quality and efficiency of the die casting process. They provide the molds and tooling that shape the molten metal into the desired form. High-quality tools are essential for:
- Consistency: Reliable tools ensure that each part produced is uniform, reducing waste and variation.
- Durability: Well-manufactured tools withstand the high pressures involved in the process, leading to longer production runs.
- Precision: Accurate molds contribute to the dimensional accuracy of the final products.
- Cost-effectiveness: High-quality tools minimize downtime and reduce production errors, leading to lower overall costs.
Why Quality Matters
Choosing a high-quality die casting tool manufacturer has far-reaching implications for your business:
1. Enhanced Product Quality
The quality of the die casting tools directly influences the end product. Poorly manufactured tools can lead to defects such as:
- Surface imperfections
- Dimensional inaccuracies
- Increased scrap rates
By investing in quality tools, manufacturers can avoid these pitfalls and produce superior products that meet customer expectations.
2. Increased Production Efficiency
Efficiency is critical in manufacturing. A reputable die casting tool manufacturer will provide tools designed for optimal performance. This translates to:
- Faster cycle times
- Reduced maintenance downtime
- Less energy consumption
By enhancing efficiency, manufacturers can increase their output without compromising on quality.
3. Competitive Advantage
In today's competitive market, having a reliable die casting process gives businesses a significant advantage. Quality tools enable quicker time-to-market and the ability to meet client demands promptly, setting your company apart from less efficient competitors.
Factors to Consider When Choosing a Die Casting Tool Manufacturer
When selecting a die casting tool manufacturer, several key factors should guide your decision:
1. Experience and Reputation
Look for manufacturers with a proven track record. An experienced manufacturer is likely to possess a deeper understanding of tooling requirements and production techniques. Research their reputation through customer reviews and industry accolades.
2. Quality of Materials
The longevity and effectiveness of die casting tools depend significantly on the materials used. Ensure the manufacturer employs high-grade metals and alloys that can withstand the pressures of the die casting process.
3. Technological Capabilities
Modern manufacturing requires advanced technology. Check if the manufacturer utilizes state-of-the-art machinery and software to design and produce tools. Technologies like 3D printing for prototypes and CNC machining can enhance precision and reduce lead times.
4. Customization Options
Every project has unique requirements. A quality die casting tool manufacturer should offer customization options to create molds tailored for specific applications, ensuring optimal performance and efficiency.
5. Customer Support and Service
Good manufacturers provide ongoing support and service. This includes assistance with tool maintenance, troubleshooting, and potential modifications. Reliable customer service can save your business time and money in the long run.
Conclusion
Investing in a reputable die casting tool manufacturer is one of the most critical decisions a metal fabricator can make. The quality of tools directly affects production efficiency, product quality, and overall business success. By carefully considering the factors outlined above, manufacturers can make informed choices that lead to competitive advantages and sustained growth in their sectors.
Contact Us
For businesses looking to enhance their die casting capabilities, Deep Mould offers premier die casting tooling solutions. With our focus on quality and customer service, we ensure that your manufacturing needs are met with precision and efficiency. Visit our website for more information on our products and services.